摘要:从性能与成本二个角度对钢瓶供氮、液氮罐气化供氮和药用高纯度制氮机供氮三种方式的进行比较,探讨了药用高纯度制氮机供氮是制药工业最佳选择的观点,同时解析了药用高纯度制氮机的稳定性问题。
关键词:供氮方式;药用高纯度制氮机;性能;成本;制药工业;选择;解析
目前,制药生产供氮方式大致有钢瓶供氮、液氮罐气化供氮和药用高纯度制氮机供氮三种,究竞哪种供氮方式能达到更有效提高药品质量与降低生产成本的目的?答案很明确是药用高纯度制氮机的供氮方式是最佳的选择。随着人们对药品质量与生产成本的日趋关注,药品生产企业势必在严格执行GMP的同时,也在挖潜降本,而药用高纯度制氮机的成功应用恰好凸现这二点的内含。本文将从性能与成本二个角度对三种供氮方式的进行比较,解析了当前制药工业应选择用药用高纯度制氮机供氮的观点,同时也解析了人们对药用高纯度制氮机所关注的问题。
1、从性能角度对制药工业中三种供氮方式的比较
1.1、钢瓶供氮
钢瓶供氮工艺繁琐、技术落后。缺点:氮气纯度低,含有微生物、热原等有害杂质。钢瓶氮气纯度一般为99.5%~99.9%,不能确保GMP验证对氮气的要求,有文献指出:市售的各种瓶装氮气,气中的含尘量为1140~265粒/l(≥0.3μm),而从气体发生站用管道输出的气体中含尘量大于600粒/l(≥0.3μm)。然而,药厂所用的氮气应是净化的,根据不同工艺要求在管路末端加装不同级别孔径的过滤器,一般用在制药生产用的氮气至少要求含尘量不大于3.5粒/l(≥0.5μm),对无菌制品要求是无尘、无微生物和无热原,而这正是钢瓶供氮很难保证的。所以,企业进行二次提纯过滤运行成本过高。
1.2、液氮罐气化供氮
液氮在制备时虽能在纯度上能符合工艺要求,但在分装或输送过程中,由于设备、附件、材料以及其它因素的污染,纯度很容易降低。据测定,高纯气体如99.999%以上的氮气在输送过程中由于设计、安装和维护管理的不当,可使气体纯度下降几个至十个ppm,甚至可能下降一个数量级。也有人测试过,未经特殊处理容量的气体,其含尘量一般大于1000粒/l(≥0.3μm),未经钝化处理的碳钢管道,其输送的气体含尘量大于600粒/l(≥0.3μm)。所以,液氮的纯度和含尘量也难以确保GMP验证的要求。同时,在其制备过程的管路等装置和调换贮罐等过程中很难满足安装、清洗和消毒的确认,又存在着无法验证氮气的微生物、热原等项目的缺陷。同时使用时,进行贮罐增压的过程也存在着一定的安全问题。
1.3、药用高纯度制氮机供氮
以瑞安市飞云机械厂生产的DYF系列高纯度制氮机为例,其采用了国际上通用的变压吸附(PSA)制氮流程,将压缩空气后处理系统、PSA制氮系统及气体精密过滤除菌系统有机地结合在一起,以其满足GMP验证要求。
(1)经有资质检测中心测试,药用高纯度制氮机产氮指标为:氮气纯度99.991%;含尘量0;微生物0;热原0。
(2)主机采用低碳奥氏体不锈钢容器管道及封闭式罩壳,与氮体直接接触的管路采用抛光低碳奥氏不锈钢,结构紧凑。
(3)采用前、后二级精密过滤器,吸附筒体内壁按GMP要求进行设计和制造,以确保氮气的洁净、无菌。
(4)采用PLC自动操作监控系统,有整套清洗消毒规程和符合GMP要求的验证报告,这些都能在药品食品生产过程中,由企业监管和测试基础上作出。
2、从成本角度对制药工业中三种供氮方式的比较
2.1、供氮成本计算依据
以供氮量:5m3/h为计算依据来计算每年的成本。其计算依据如表1所示。
表1供氮成本计算依据
钢瓶供氮 |
液氮罐气化供氮 |
药用高纯度制氮机供氮 |
(1)供氮气钢瓶5m3/瓶(费用约26元),以每小时用1瓶,氮气钢瓶利用率为80%;
(2)钢瓶运输费约2元/瓶,每天8h实需用瓶数为1瓶/80%×8h/d=10瓶;
(3) 气源后处理费(含过滤器、检测等)费用约4.5万元;
(4)装卸和后处理人工费(每人2万元/Y),约需3人,费用6万元。 |
(1)一个进口5m3贮罐约13万元/台,连续生产需二台(其中一台调换灌液氮),以10年折旧计算每年液氮贮罐费用为2.6万元;
(2) 1 m3液氮约可以增压为标态氮气620 m3,即1 m3液氮=620×80% m3氮气(气化利用率80%),折算为1 m3氮气价格=1000÷(620×80%)=2.02元(1 m3液氮价格约为1000元),按5m3/h量计算每年灌液氮费用2.02万元;
(3)约每12天需外出灌液氮一次,一年灌液氮贮罐运输费(运输费以300元/次计)为0.625万元;
(4)气源后处理(含过滤器、检测等)费为1万元;
(5)贮罐维修保养(含安全阀校验等维修保)费约每年0.1万元/台,费用0.2万元;(6)装卸和后处理人工费(每人2万元/Y),约需1.5人,费用3万元。 |
(1)DYF-5型制氮机投资价格为28万元/台,以10年折旧每年费用为2.8万元;
(2)配空压机与附助管路设备投资(国产设备约3万元,加管路估0.5万),以10年折旧每年费用为0.35万元;
(3)运行电费(制氮机1kW,空压缩机7.5kW,电费0.70元/度),每年制氮机用电费为1.19万元;
(4)气源后处理(含过滤器、检测等)费为0.5万元;
(5)操作工人工费(每人2万元/Y),约需0.5人,费用1万元;(6)机器维修保养费(含制氮机与空压缩机)约为0.6万元。
|
2.2、三种供氮方式成本计算与比较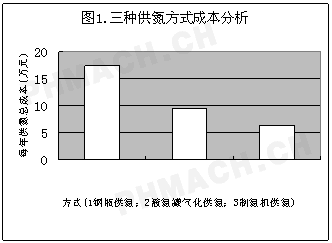
计算过程从略,其结果:
(1)钢瓶供氮方式的每年总成本约17.5万元;
(2)液氮罐气化供氮方式的每年总成本约9.445万元;
(3)DYF系列药用高纯度制氮机供氮的每年总成本约6.45万元。
从图1中可知:当氮气需要量为5 m3/h时,选用DYF-5型药用高纯度制氮机后,每年单班生产,比液氮钢瓶供氮节约2.905万元,节约的费用9年多就可收回投资;比传统钢瓶供氮节约10.96万元,节约的费用2年半就可收回投资。如每年两班生产则节约效果更为显著。
3、为何制药工业应选择用药用高纯度制氮机供氮?
(1)前几年国家药监局对安徽华源公司“欣弗事件”调查结果为:违反规定生产,是导致这起不良事件的主要原因,同时“欣弗”做无菌检查和热原检查不符合规定的结论。这一事件给制药企业敲响了确保药品生产任何环节质量的警钟,不要以为类似于最终灭菌药品生产的最后环节能灭菌,其它环节就能放松,换句话而言制药生产的任一环节均应严格控制。然而,制药生产用氮却是无菌制剂生产的重要环节,从严格意义而言,传统供氮方式在生产工艺过程中存在着一定难以控制的环节,稍有疏忽将严格影响到药品的质量。
由于GMP的目的在于确保药品生产全过程的各个环节,都有法规、标准之类文件加以约束,从而使最终产品的质量达到安全、有效、均一。而上所述的钢瓶供氮与液氮气化供氮方案在纯度、含尘量、微生物和热原等控制方面难以用验证的方法予以确保,在这些供氮方案的使用过程中,有部分厂家靠单一过滤器来滤除含尘量、微生物和热原等,但事实上是无法真正确保除去微生物和热原,因为有权威文献认为:过滤器能够滤除绝大多数细菌和真菌,但不能全部滤除病毒和支原体。同其他灭菌方法相比较,过滤灭菌法风险更大。这说明了单一过滤法有潜在风险,所以应使用双重过滤法进行过滤。而氮气质量控制过程都压在未道的过滤上,其除去微生物和热原过程不是全过程的控制,难以确保每一个环节的可说明性。
(2)“欣弗事件”事件有一个教训值到人们吸取,那就是生产过程记录与验证的不完整,对制药生产用氮过程而言,传统供氮方式的最大缺点便是氮气的制备过程是不能记录与验证的,因为其是其它工业级生产单位所供应的。然而,药用制氮机却能弥补这一遗憾,以瑞安市飞云机械厂生产的DYF系列药用高纯度制氮机为例,其采用先进的电脑过程控制,可实现无人值守,配有KY-2N在线分析仪,非常直观方便,确保了氮气的质量。在采用前、后二级精密过滤器以确保氮气的洁净、无菌和无热原的同时,有整套符合GMP要求的验证报告范本,这些都能在药品生产过程中,由企业监管和测试上做出,可做到氮气制备的全部过程可记录、可控制和可验证,这也是其质量控制可追溯性和可说明性的关键体现。
(3)以瑞安市飞云机械厂生产的DYF系列药用高纯度制氮机为例,其氮气制备从源头上就开始就对空气进行过滤(即空气压缩机进口外过滤,过滤器过滤精度0.3μm),再经冷干处理进入制氮机制氮,在进入制氮机前又设有0.3μm灭菌过滤器,当氮气出制氮机时出口精密灭菌过滤器过滤精度0.01μm。这样的前、中、后三级精密过滤器设置与氮气吸附筒体内壁按GMP要求进行设计和制造,从源头到制备整个过程的控制,均能确保氮气的洁净、无菌,这些严格的过程控制是其它供氮方式所无可比拟的。
由此看来,用药用高纯度制氮机对制药生产供氮能确保用生产中氮气质量达到安全、有效与均一的目的,也是众多供氮方式中最佳选择。
4、影响药用高纯度制氮机稳定性的解析
药用高纯度制氮机是采用PSA原理制备的,对此类制氮机能否长期稳定的运行与生产出合乎技术要求的氮气是众所关心的问题,而影响制氮机稳定的因素主要有三个方面:
(1)碳分子筛:它是PSA制氮机的核心和关键。制氮技术上要求碳分子筛强度好、产氮率高、氮气的纯度与回收率大。诚然,碳分子筛的质量和性能是关键,但是在碳分子筛的选用上也很有讲究。在碳分子筛的选择上,瑞安市飞云机械厂生产的药用高纯度制氮机采用国际著名品牌的德国BF公司或日本武田公司的分子筛,其具有颗粒均匀、硬度高、使用寿命长以氮气产量高等优点,使用者均可放心使用,当使用若干年后,只要调换碳分子筛就可继续使用,且调换碳分子筛的价格与使用其它供氮方式相比更是不屑一顾。
(2)在制氮机的设计也很有讲究的,若结构设计不当就会因高速气流的冲击产生分子筛的跳动和相互磨擦而粉化失效。而瑞安市飞云机械厂生产的药用高纯度制氮机,在吸附塔底部设置气流分部器,在顶部设置压紧装置,有效地此现象的发生。
(3)由于大气污染的存在,空气中的油蒸汽容易被碳分子筛所吸附,并难以脱附,填塞微孔而使分子筛失效。另外,水对碳分子筛而言虽然不是致命的,但会使碳分子筛“负荷”增加,即影响其吸附O2、CO2等气体的能力。因此,瑞安市飞云机械厂生产的药用高纯度制氮机装置在配套时,空压机进口前端就配有油水分离器和前端的精密过滤(其一则除菌,二则分离油)。这样将压缩空气进行除油与冷冻干燥除水处理,将有效地提高了分子筛吸附能力和稳定性。
4、结论
本文从性能与成本二个角度对钢瓶供氮、液氮罐气化供氮和药用高纯度制氮机供氮三种方式的进行比较,探讨了药用高纯度制氮机供氮是制药工业的最佳选择的观点。可以得到这样的结论:无论从控制生产过程与严格执行GMP,还是降低生产成本,用药用高纯度制氮机供氮是制药工业的最佳选择。
参考文献:
1丁金文.药品食品使用氮气方案的分析和制氮机的验证.中国制药装备杂志.总No5.2004
2缪德骅主编.药品生产质量管理规范实施指南(2001).化学工业出版社.2001
3叶瑛瑛主编.药品生产验证指南.中国医药科技出版社.1996
4叶大进等.药用高纯度制氮机的基本原理及在制药工业应用的探讨. 制药机械杂志.No200,2005
本文摘编于:田耀华,对药用高纯度制氮机应用的解析.制药机械杂志[J].207期. 2006(10)